Sub-industry
Civil Asset
Problems
Subsidence
Location
Auckland
Year
2024
Solutions
Ground Improvement
Technology
Teretek® Ground Improvement
Mainmark’s quick, cost-effective ground improvement solution prevented further subsidence in this Auckland suburb, saving Auckland Council time and money.
Background
Auckland Council had received repeated complaints about the subsidence of the footpath outside a home in Auckland’s Northcote suburb. The footpath sat on top of a wastewater asset and manhole owned by Watercare, New Zealand’s largest water utility.
The homeowner had experienced repeated damage to their fence due to the reoccurring subsidence within a 5-year period. After resurfacing the path and repairing the compromised fence multiple times, Watercare decided to look for a more permanent solution.
Problem
Geotechnical investigations showed that this repeated issue went deeper than initially anticipated, and in fact initiated around the base of the manhole, between 6-8m BGL (below ground level). Groundwater flows had washed out the loosely consolidated soils around the manhole, resulting in the loss of support and subsequent damage above ground.
Traditional repair methods for this issue would include deep excavation and lengthy road closures at great cost. In search of a cost effective and time efficient solution, Mainmark was called in to collaborate and consult.
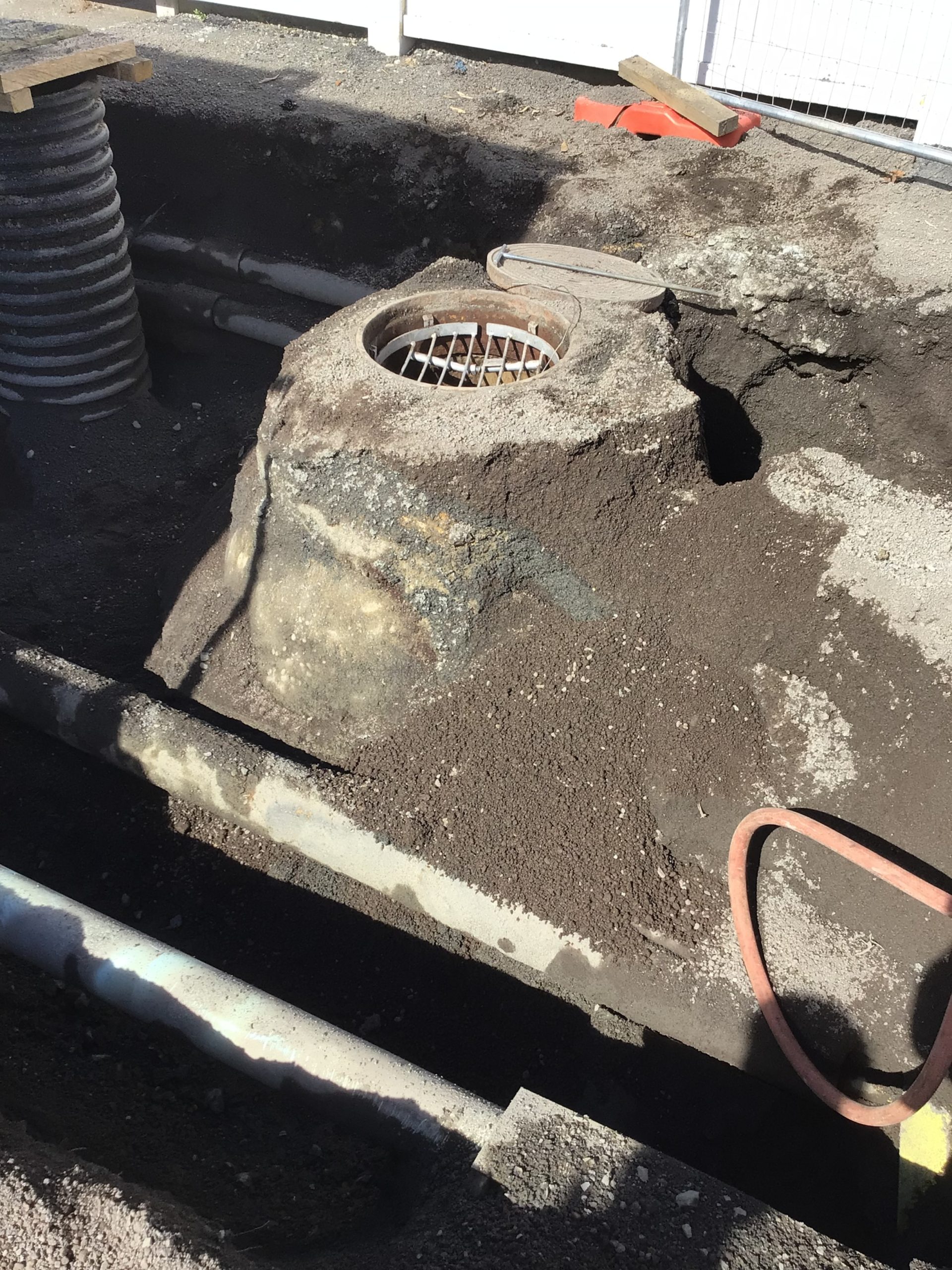
Solution
Using Teretek resin injection, Mainmark was able to target the layer between 6-8m BGL. This process was done to densify the loose soil and subsequently increase the bearing capacity of the soil to mitigate further subsidence.
As with all underground services, there is a small window of tolerance for the amount of movement that can be induced on a manhole or in/out going pipes. To overcome this challenge, a resin with a slower expansion rate was used. This resin was able to permeate the loose soils and fill the voiding caused by groundwater washout, without inducing significant vertical movement on the manhole.
Outcome
Ground investigations such as CPTs (Cone Penetration Test) and DCPs (Dynamic Cone Penetrometer) were used to validate the works completed. Test results indicated a successful outcome, showing an increase of the qc (CPT Cone tip resistance) and the blows per 100mm on the DCPs within the injection zone.
Mainmark’s solution was delivered within 2 working days, and ultimately came in at a fraction of the cost of an alternative solution.