Owners in manufacturing and heavy industries will be familiar with the daily wear and tear their facilities experience.
Sunken floors or misaligned concrete slabs are especially common, with forklifts or other heavy vehicles on site. Over time, this can impact productivity as well as employee health and safety. Mitigating these risks before they get worse means you avoid having to respond to fatal incidents after the fact.
There are many reasons to take a proactive approach to fixing wear and tear: increased productivity from reduced incidents, more efficient operations, and preventing any further damage to the property.
Industry organisations also highlight the importance of making health and safety a part of business as usual to save lives. Recent statistics show that New Zealand has 4x as many work-related deaths and injuries as the UK. Closer to home, Australia’s workplace fatality rate is half that of New Zealand’s*.
Being proactive about the condition of your facilities isn’t complicated. The first step is simply noticing the signs that might indicate more serious issues.
What should workers and owners look for?
There are many different causes of subsidence but all involve some change in the ground which generates movement of the soil. Looking for early signs means preventing further deterioration and avoiding expensive, hard-to-fix damage to buildings and other structures.
New trip hazards or presence of surface water. Sunken or unlevel slabs in warehouses or logistics facilities can be a sign of ground subsidence. You may notice a new trip hazard from uneven slabs or, if they cause water to pool in certain areas, an increase in surface water hazards.
Machinery malfunctions start to occur. If an area is a hardstand for equipment, uneven floors can result in machinery becoming misaligned. Some sensitive equipment can stop functioning correctly, causing disruptions as well as warranty issues.
Forklifts or other warehouse traffic experiencing jolts. Over time, traffic can cause deterioration of the slab edge. The resulting misaligned concrete slab joints are a hazard for forklift operations. As the forklift travels across the step between the slabs, a jolt can cause the load on the fork to move.
Driveways & truck yards experiencing erosion. Open slab joints allow rainwater to infiltrate the subgrade beneath the transport yard pavement. As trucks travel across the slab, the soil fines are pumped out from underneath the slab, removing the slab’s support. Over time, the void beneath the slab increases.
Machinery vibrations causing too much movement in the floor. Vibrations from machinery can cause the founding soils to settle and base slabs to subside. In extreme cases, vibrating machinery can cause the surrounding slab to bounce up and down.
There are many other signs that may be harder to look for, but these conditions can increase the risk of subsidence at your facilities:
- Significant wear and tear from heavy loads, machinery vibrations, and continual use.
- Environmental and weather conditions like moisture, salinity in coastal areas, and seismic activity.
What to do if you notice these signs
Filling large voids and holes will re-level and support sinking slabs or floors, reducing costly operational and safety issues.
In cases where repair and maintenance is needed, maintaining operational efficiency is crucial. Any downtime in this sector can result in significant financial losses. It can also be important to ensure machinery stays within tight operating tolerances.
Mainmark are experts in helping factory and warehouse owners faced with unlevel buildings and weak ground. Our Teretek and JOG solutions are controlled, fast, and low impact with minimal business disruption. The works are minimally invasive, and we avoid costly and disruptive excavation or underpinning. Projects can be completed in as little as a few days or even a few hours, with floors trafficable within the same day.
Mainmark solutions are non-toxic, environmentally inert, and safe for surrounding water sources. We also have experience carrying out works while keeping to strict hygiene standards, as required in industries such as agriculture, horticulture, viticulture or seafood.
Returning foundations back to level will correct uneven floors and remove trip hazards. Mainmark can also re-level storage tanks and silos to avoid costly demolition or rebuilds.
Ground improvement ensures manufacturing facilities can support heavy loads and machinery vibrations. We improve the load-bearing capacity of soil under your structures to increase foundation performance and reduce long-term subsidence.
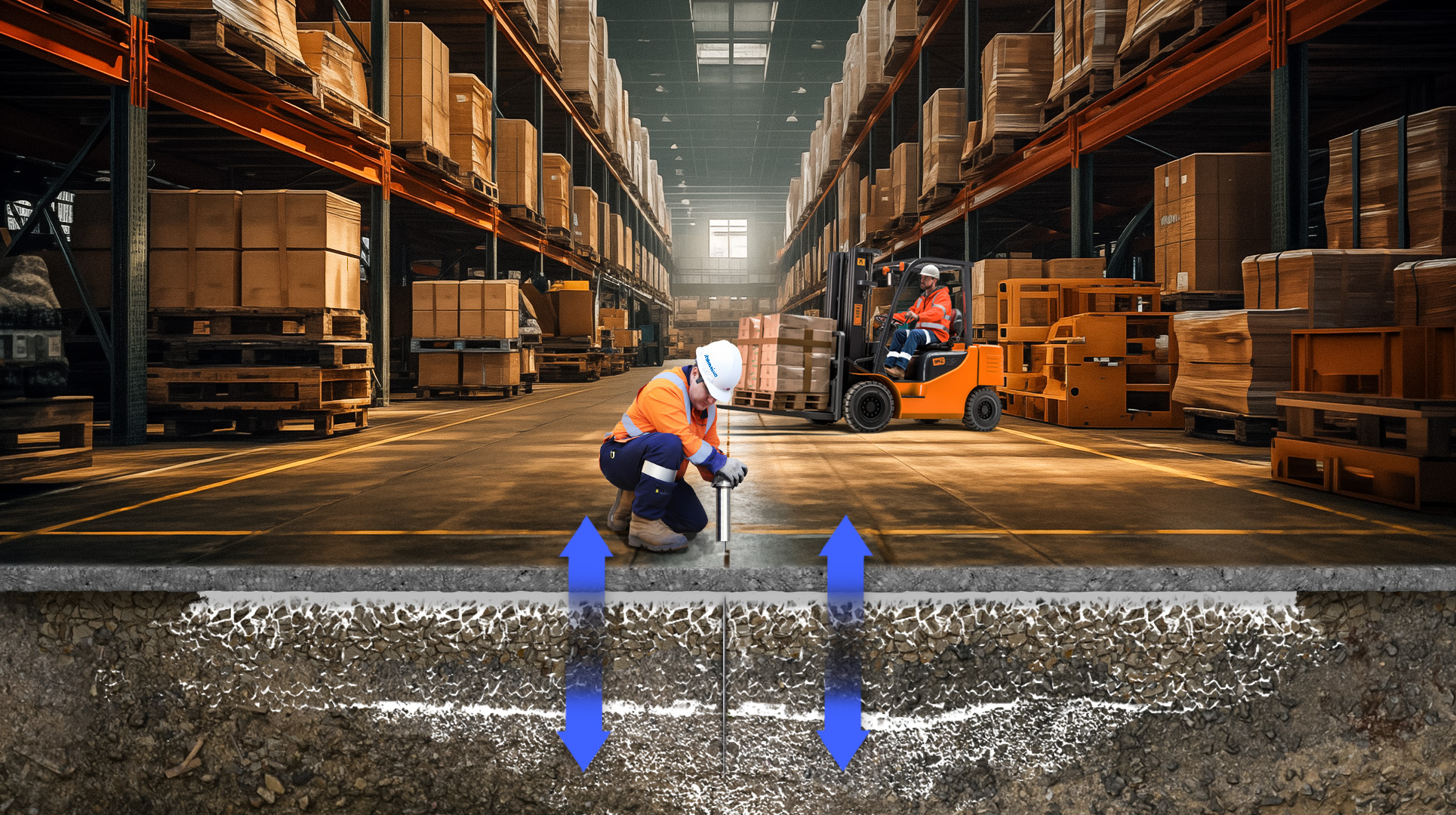
Owners of warehouses, manufacturing and heavy industry facilities often manage many risks and maintenance concerns. Subsidence from natural causes or wear and tear from machinery operation is to be expected. Mitigating these risks before they get worse means you can avoid negative impacts to productivity as well as employee health and safety.
A proactive approach ensures staff safety as well as the efficiency, safety, and longevity of your facilities.
*These are two comparable nations that use risk-management frameworks (data from the Business Leaders’ Health and Safety Forum).